![]() Patrik Holm |
If you’re considering a shaft generator or propulsion motor for your vessel design, you already know you’ll be saving on fuel consumption, improving efficiency, and complying with the current EEDI and EEXI emission limits.
With an electric machine on the shaft line, we face new considerations in shaft line dimensioning. The bearings in the shaft line are common to both the shaft line and the electric machine, and the shaft line is directly connected to the machine rotor. Thus, torsional vibrations, lateral vibrations and rotor deflection must be considered.
Thorough support
We at Yaskawa Environmental Energy / The Switch thoroughly support customers in every aspect of the planning and installation of our electric machines. We provide detailed technical notes and the necessary input data and design limits required for accurate analyses by the shipyard and its shaft system designers. And we’re available for consultation at any time throughout the process.
Specific issues to be considered in shaft line dimensioning include:
1. Torsional vibrations in the shaft line
There are torsional excitation frequencies in the electric machine, which originate from the interaction of the rotor permanent magnets with the stator slots – so-called torque ripple.
However, most of the torsional excitations derive from the combustion engine and the propeller. These torsional excitations must not exceed the design limits of the PM machine.
2. Vibration excitations from the electric machine
There are excitation frequencies in an electric machine that originate from the fundamental electrical frequency and its harmonic orders/multiples.
Vibration response is reduced by damping. There is a damping effect from electromagnetic forces in the air gap between the rotor and stator. These electromagnetic forces act as a negative spring force in the air gap – in other words, as tension springs with negative spring ratio.
Typically, there are several natural lateral frequencies below 50 Hz in the shaft line. This means it is very likely there will be resonance somewhere over the variable-speed operational range. If necessary, the control system will take account of these by avoiding operation at certain rotational speeds. It is most important to avoid lateral resonances in the nominal speed operational range of the vessel by designing the natural frequency of the shaft system accordingly.
3. Rotor deflection within the stator due to external dynamic accelerations
There will be an initial eccentricity between the stator and rotor due to inaccuracy in the air gap measurement and eccentricity adjustment.
This eccentricity has an impact on rotor deflection within the stator, both statically and dynamically. Meanwhile, when the vessel is exposed to external accelerations, the electric machine rotor will also move within the stator.
The unbalanced magnetic pull (UMP) forces increase due to the negative air gap stiffness, resulting in a further strengthened rotor deflection that requires sufficient stiffness in the shaft line.
How much shaft line stiffness is sufficient differs for each vessel design and depends on specific bearing spans, bearing stiffnesses, shaft diameter, shaft mass, machine rotor mass, negative stiffness in the air gap and external accelerations.
Detailed data for analysis
We provide detailed information for customers on each of these topics, including a careful discussion of the contributing factors, specific tests and verifications to plan for and numerical input data.
Please download our technical note for a more extensive discussion of these issues and don’t hesitate to get in touch if you have further questions. We are here to help.
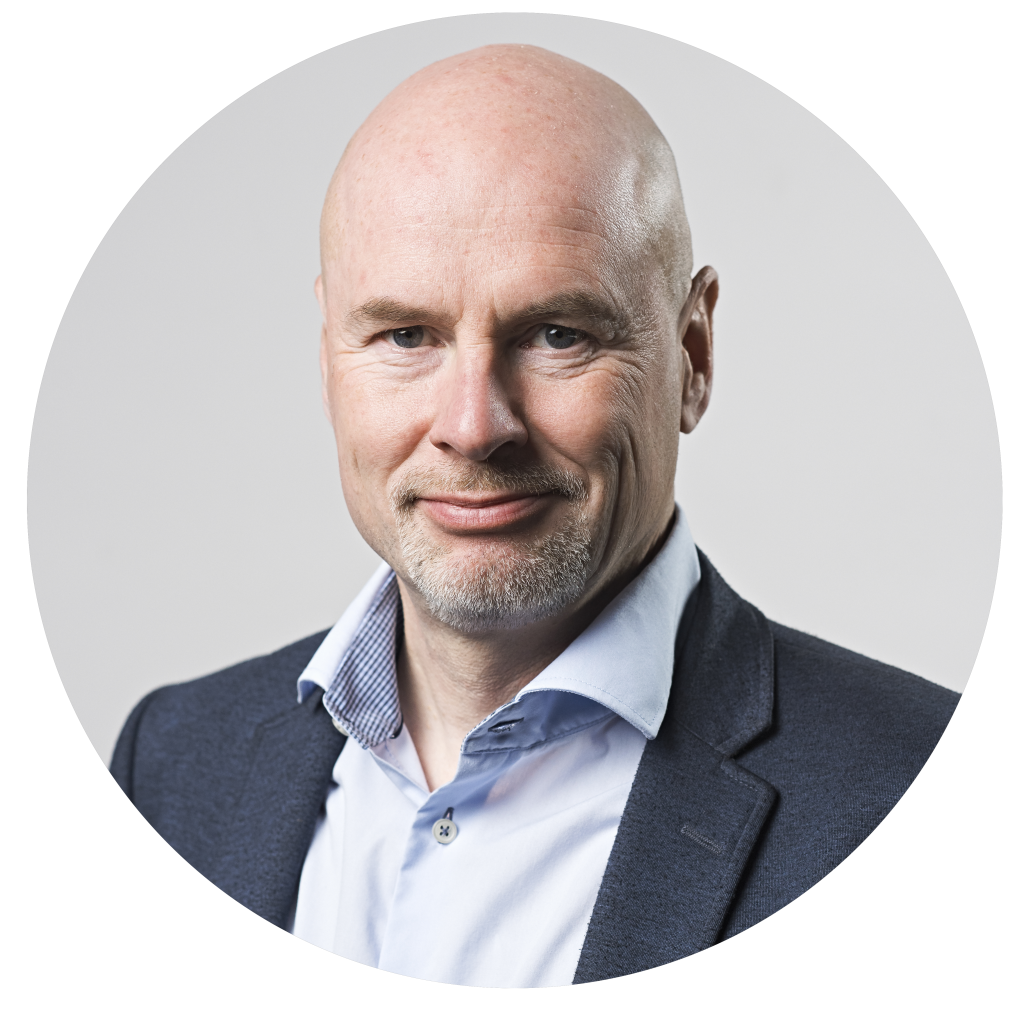
Patrik Holm
Senior Manager, Special Engineering, Electric Machines, Technology
at Yaskawa Environmental Energy / The Switch, Finland
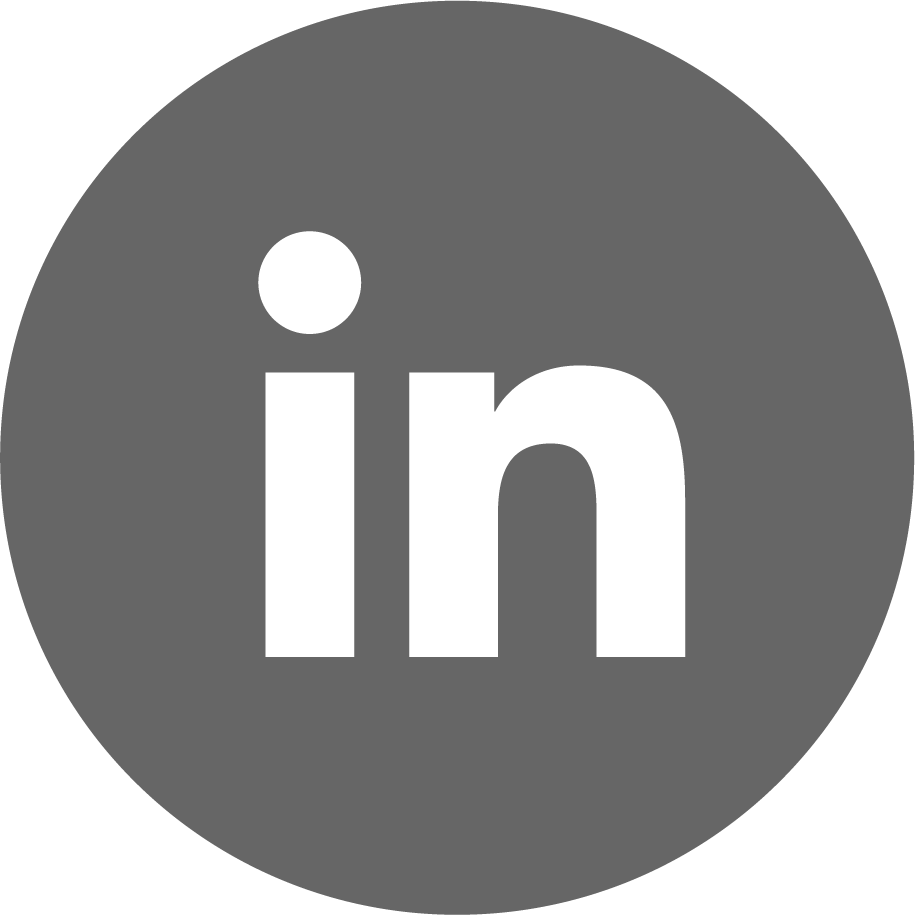
Patrik Holm, BSME, has been involved in the energy business and machinery product development for his entire 35-year career. He spent more than a decade developing diesel engines for marine and power plants, a second decade with various engineering projects for the energy industry and a third decade developing a multimegawatt direct-drive wind turbine. Common to all of these applications is the electrical machine. These machines generate the power for consumption and propulsion that are the core business of Yaskawa Environmental Energy / The Switch, and this is now Patrik’s main engineering responsibility.