Looking at my email history, I see that the term “shaft generator” first appeared in my email conversations in May 2013. So, it has been exactly ten years to date from when we first started to think how we could utilize our permanent magnet technology originally developed for the wind industry in marine applications – a completely new field for us.
Back then, we didn’t know very much about marine applications or requirements. Although, we had the experience of building two custom-made gensets. However, we heard about a machine called a shaft generator from our soon-to-be partner WE Tech Solutions, a Finnish system integrator who had just jumped into this business.
And so, we started to dive into the specifics of this application. It appeared to be a generator wrapped around a ship’s propulsion shaft. The system utilizes a vessel’s more efficient two-stroke main engine rather than four-stroke gensets, which were more common back then in large vessels.
Why shaft generators?
Shaft generators were first introduced in the 1960s. Their main advantage is the better fuel economy of a two-stroke engine technology compared to four-stroke technology. When electric power is produced with a slow-speed main engine instead of medium- or high-speed gensets, this results in significant fuel savings.
Originally, shaft generators were based on electrically excited synchronous machines (EESMs). In this case, external energy is needed to create the magnetic field linking the stator and the rotor. The main drawback of EESMs is their rather low efficiency. Especially in slow-speed applications, where the primary power must come from the main engine, this leads to increased fuel consumption.
PM technology – efficient alternative
When we realized that the propulsion of large vessels typically runs at rather slow speeds of 40–100 rpm, our first thought was that permanent magnet (PM) technology could really make a difference for these systems. This is because the lower the operational speed of the generator, the bigger the efficiency gain of PM machines over conventional machines. PM machines are best suited for slow-speed applications.
We had already made various PM generator designs for direct-drive wind turbines, running typically between 10 and 20 rpm. Based on our rough calculations, a vessel’s lifetime fuel savings from the difference in generator efficiency might be up to USD 2 million, depending on vessel type and operational parameters. This means a very short payback time and significant savings for the operator during the vessel’s operational lifetime. Therefore, we quickly started to study more about shaft generators – and the best ways to utilize our existing technology in this new application.
Overcoming the challenges
Since we didn’t know much about marine-specific requirements, our first impression was that we could simply mechanically modify our existing wind generator design to be connected to a vessel’s propulsion shaft.
This was rather wishful thinking. There was a good reason why nobody had made inline shaft generators with PM technology before. The fundamental feature of any permanent magnet machine is that the magnetic field is indeed permanent. This means that it cannot be switched off, for example, in case of a short circuit in the stator winding. Since the shaft generator is mechanically fixed to the propulsion shaft, excessive fault current will flow and pose a risk of catastrophic failure as long as the propulsion keeps running. In turn, stopping the whole propulsion because of a generator failure was a big no-no since the vessel would be left drifting out in the sea.
This issue does not apply to a conventional electrically excited generator. There, the magnetic field can be easily shut down by stopping the supply of the external magnetization current in the case of a generator short circuit.
Due to this potential risk related to PM technology, the first reaction from some classification societies and one major generator manufacturer was that using PM technology in such an application would never be accepted.
But since we had already done quite unique things in wind, we were confident that there must be a workaround to make the shaft generator system based on PM technology adequately safe for use in large vessels. By adding a few special design features to our machines, we were soon able to convince various stakeholders, including shipowners, operators and classification societies, that the technology really works without any safety concerns.
Since the shipping industry has always been very conservative, it took endless meetings and discussions to gain stakeholder support. But in the end, it was worth it.
In 2014, we successfully tested our first PM shaft generator in our Vaasa factory and delivered four of those to WE Tech, who had sold the whole shaft generator system to car carriers owned by Wallenius Lines AB. After successful factory acceptance tests, our machines were certified by Lloyd’s Register and delivered to the shipyard located in China. Below is a picture of these machines during full-power tests.
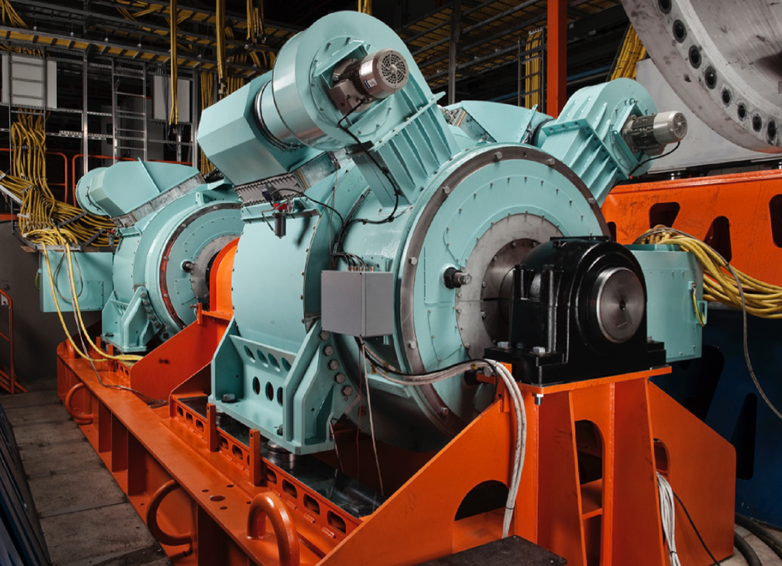
PM efficiency in line with emissions regulations
After the successful delivery of these first machines, more customer orders started to follow. Shipowners realized the full potential of this new technology.
During the first 5 years in this business, our deliveries were rather stable – and modest. At the same time, it was becoming obvious that vessel emission regulations would be significantly tightened, forcing shipowners to drastically cut their vessel’s CO2 emissions.
While in the beginning the main reason for choosing PM technology was driven by economics due to fuel savings, it soon became apparent that the reduction of greenhouse gases (GHG) would soon play the main role when deciding which technology to use.
Two new measures implemented by the International Maritime Organization (IMO) came into force on 1 January 2023. The new Carbon Intensity Indicator (CII) and the Energy Efficiency Existing Ship Index (EEXI) are forcing shipowners to take drastic measures to lower their GHG emissions. Permissible emissions will decline year after year, and vessels that cannot demonstrate compliance with CII and EEXI may not be able to trade internationally. This means that shipowners have no choice but to lower their fleet’s emissions.
Due to these new regulations, we saw a huge increase in our shaft generator delivery volumes starting from 2020, and annual bookings have greatly increased year after year since then.
Scalable design and LDTC for optimal customized deliveries
Just before this recent boom, we had made a significant redesign of our shaft generator technology plus a couple of other important decisions.
First of all, there were countless improvements based on years of field experience. But more importantly, we made the whole design much more modular and scalable. With this, we could now make fully optimized, tailor-made designs with just a small amount of extra engineering. This is vital in this business since deliveries per project are often small – can even be only one machine. So, we had to be able to make the needed changes with as minimal engineering effort as possible while still delivering a fully optimized machine to the customer. This also means we can keep delivery times rather short, which is also critical.
What’s more, we made a significant investment in our Lappeenranta testing facilities. Once the new Large Drive Test Center (LDTC) was opened in 2020, we were able to test the machines at full power up to 18 MW, which is unique even on a global scale. The LDTC also allows the so-called string testing, where we can connect the customer’s frequency converters to our test system and verify the performance of the generator and frequency converter system as a whole. This ensures that no negative surprises appear during commissioning when it is way too late and expensive to start redesigning anything. And with an upgraded crane capacity of up to 100 tons, we are now able to build and test very large machines.
Additionally, we developed a completely new and bigger frame-size machine, PMM1500M, which is mainly intended for large LNG carriers and similar-size vessels. And we also started the design work for an even bigger PMM2000M machine, mainly aimed at large container vessels.
All these developments and investments have consumed a great amount of money and resources. But currently, we are very well positioned from our product and manufacturing capacity perspective to meet the increasing demand for efficient power generation technologies driven by the huge maritime industry tailwind – decarbonization. The following picture shows our latest shaft generator design in different sizes.
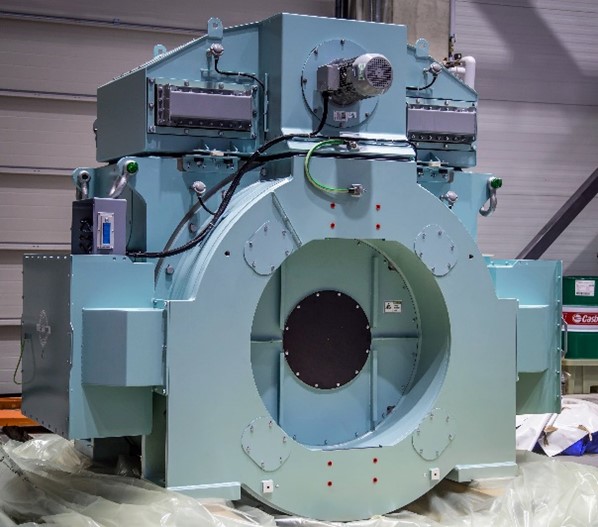
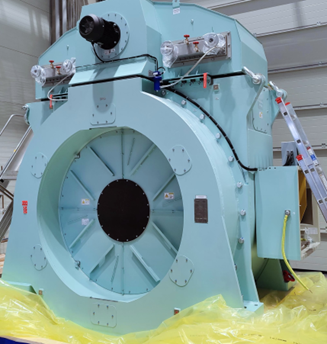
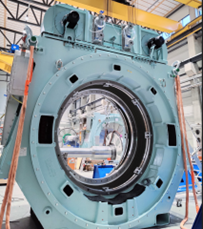
From left to right: PMM1000M, PMM1500M and PMM2000M. These machines can cover the power rating from under 1 MW up to 12 MW in shaft generator and propulsion applications. The appearance of these second-generation machines is quite different from where we started due to their optimized and scalable design.
The future of shipbuilding
While shipbuilding has traditionally been a boom-and-bust type of business, we believe that the trend of green technologies will only be ticking upward for years to come.
While we might have been over-optimistic in the beginning when we thought that we could simply use our existing wind products with some minor modifications, some people, on the contrary, were too pessimistic, believing that this technology would never be approved. Yes, it took 5+ years before this new business really started to ramp up – and, probably, not a single component is left from the wind application. But to me, it has still been surprisingly fast. It is difficult to change conservative industries such as marine, but when the change happens, it happens fast. This we have already seen in the wind business, where all the top 10 most powerful wind turbine designs are nowadays using PM technology. Two decades ago, this number was zero.
Usually when there is a clear need for a disruptive technology in any industry, engineers can often make near miracles. And soon, these “novel” technologies become mainstream replacing older ones. If nobody were willing to take the risk of adopting new technologies, mankind would probably still be in the Dark Ages.
In the same way cars with internal combustion engines are headed for extinction, being replaced with electric ones, permanent magnet shaft generators are rapidly replacing conventional-type generators in large ocean-going vessels. Not only will PM shaft generators help in significantly lowering the vessel’s greenhouse gas emissions, they will also contribute to significant monetary savings through lower fuel consumption. What shipowner wouldn’t want to make their fleet cleaner while simultaneously saving large chunks of money?
PM shaft generators forge ahead
As of 2023, we have well beyond 100 inline shaft generators in operation to date, with several million cumulative operating hours and no technical issues leading to vessel downtime. The first ones have been running reliably since 2015. This proves that the technology is truly sound.
Even though we heard many concerns in the beginning that PM shaft generators are doomed to fail, we never had any doubts that they would be a viable option. As in life in general, nobody knows your business better than you do. Therefore, you should always trust yourself and not put too much emphasis on the comments from the outside.
The following chart shows our cumulative inline shaft generator orders from day one to this day. Not a bad achievement, considering that we basically started this business from scratch – although the core of this solution has been in use in our company for 20 years.
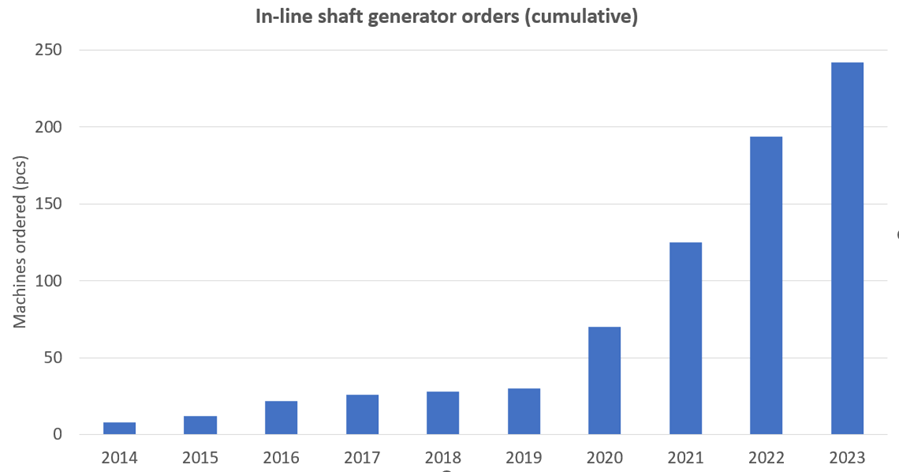
Come meet us at the Electric & Hybrid 2023 expo in Amsterdam to find out more about our PM shaft generators!

Product Line Director, Electric Machines
Jussi Puranen

Jussi has nearly 2 decades of experience in R&D and product development of electrical machines, and his main responsibilities are the product management and R&D of electric machines (especially PM machines). Puranen holds an M.Sc. (Technology) degree in Electrical Engineering and a D.Sc. (Technology) degree from the Lappeenranta University of Technology (LUT), Finland.